Page 1 of 9
XPS and Epoxy

Posted:
Wed Jan 04, 2023 10:02 pm
by kstills
I just watched a video of a guy using XPS, E grade Fiberglass and Epoxy that ended up making a smooth finished structural part that would be perfect for constructing the cabinetry in my van. Am I right in assuming that the reason this method isn’t promoted here is related to the cost of the epoxy and not to how good an adhesive bond will be formed?
Re: XPS and Epoxy

Posted:
Wed Jan 04, 2023 11:29 pm
by tony.latham
Am I right in assuming that the reason this method isn’t promoted here is related to the cost of the epoxy and not to how good an adhesive bond will be formed?
I keep suggesting this over PMF. In the aircraft world, this is called moldless construction. Epoxy adheres to the foam just fine.
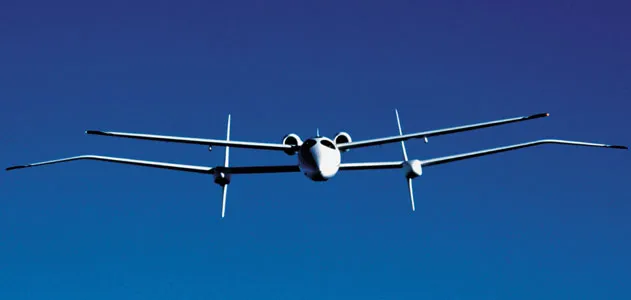
Burt Rutan pioneered the process.
Tony
Re: XPS and Epoxy

Posted:
Thu Jan 05, 2023 12:59 am
by kstills
Tics all the boxes for mr; strong, lightweight, you can get a smooth finish with practice and you can paint over it. Interiors can be done cheaper, but the outside id want a nicer look.
Re: XPS and Epoxy

Posted:
Thu Jan 05, 2023 7:22 am
by GPW
"you can get a smooth finish with practice " ...
Best try this on scraps first ...

Re: XPS and Epoxy

Posted:
Thu Jan 05, 2023 7:25 am
by kstills
So a big question I have is whether or not I need to reinforce the stress points where I'll be putting hinges and struts. I see I can buy different gauge fiberglass which will create different levels of structural integrity, but I have zero practical knowledge of how this works long term with repetitive actions like opening and closing doors (drawers I think will be less stress overall). I could certainly integrate some ply into the foam, but obviously if that's not necessary I'd like to avoid it.
Re: XPS and Epoxy

Posted:
Thu Jan 05, 2023 7:30 am
by kstills
GPW wrote:"you can get a smooth finish with practice " ...
Best try this on scraps first ...

https://www.youtube.com/watch?v=3Pc-Sd_J26EThat's the vid I watched. In it, he describes how to get a smooth finish over the fiberglass mat. The trick, according to him, apply epoxy to the foam, then lay the mat overtop. The epoxy will wick up through the mat and create a bond devoid of air bubbles. He doesn't even rub out the mat, he just lets it soak onto the foam/luan. Then, he allows the epoxy to just come to set, where it doesn't tack off the board but it hasn't fully cured, then applys the top coat of epoxy. That's the one that bonds and flows out smooth.
As I'm not a painter of any kind, I will be practicing this technique on the interior bits before doing the more visible exterior portions.
Re: XPS and Epoxy

Posted:
Thu Jan 05, 2023 8:38 am
by Pmullen503
kstills wrote:So a big question I have is whether or not I need to reinforce the stress points where I'll be putting hinges and struts. I see I can buy different gauge fiberglass which will create different levels of structural integrity, but I have zero practical knowledge of how this works long term with repetitive actions like opening and closing doors (drawers I think will be less stress overall). I could certainly integrate some ply into the foam, but obviously if that's not necessary I'd like to avoid it.
Just like with PMF you will have to incorporate something to hold fasteners. A strip of wood to hold hinges screws. If you have through fasteners, something like a dowel with a hole drilled through it so you can tighten a bolt without crushing the foam underneath.
Re: XPS and Epoxy

Posted:
Thu Jan 05, 2023 8:53 am
by RJ Howell
Pmullen503 wrote:kstills wrote:So a big question I have is whether or not I need to reinforce the stress points where I'll be putting hinges and struts. I see I can buy different gauge fiberglass which will create different levels of structural integrity, but I have zero practical knowledge of how this works long term with repetitive actions like opening and closing doors (drawers I think will be less stress overall). I could certainly integrate some ply into the foam, but obviously if that's not necessary I'd like to avoid it.
Just like with PMF you will have to incorporate something to hold fasteners. A strip of wood to hold hinges screws. If you have through fasteners, something like a dowel with a hole drilled through it so you can tighten a bolt without crushing the foam underneath.
Agree with Pmullem, adding structural components as needed. I'm going to rebuild my roof and this time around I plant to rout in these components. Placing between causes differences in materials that's difficult to echo through the finish product. Around doors/windows/vents I'd use full width due to flanges covering and no collapse of material. Same principles to make cabinets. I still would not do this for a floor!

Re: XPS and Epoxy

Posted:
Thu Jan 05, 2023 8:58 am
by kstills
If you watch the video I posted, the guy beats on the glassed foam with a heavy metal ball and doesn't dent it at all. I think I'll mock one up, bolt through both sides and see how much it compresses when I tighten it down. Given that a screw passing through the mat into the foam will only have that tiny layer of epoxy-glass to grip, I don't see that method holding up long term, but if I can get decent compression with a nut and washer on the other side, that might provide a way to avoid the engineering required to provide all those wooden supports where I'm going to need them.
If it doesn't work, well, construction will simply take longer lol.
Re: XPS and Epoxy

Posted:
Thu Jan 05, 2023 9:33 am
by kstills
So I ordered some 72 hour cure epoxy and the E grade fiberglass as well as a 24oz mat. I'll mock up both and see what happens.
Re: XPS and Epoxy

Posted:
Thu Jan 05, 2023 10:01 am
by Pmullen503
Inset plywood eventually telegraphs through. I put it down to different thermal expansion coefficients. Using splines like you show should eliminate that.
Re: XPS and Epoxy

Posted:
Thu Jan 05, 2023 10:14 am
by kstills
Pmullen503 wrote:Inset plywood eventually telegraphs through. I put it down to different thermal expansion coefficients. Using splines like you show should eliminate that.
Could I get an explanation here?
Re: XPS and Epoxy

Posted:
Thu Jan 05, 2023 10:46 am
by Pmullen503
See how the door frame shows? It was flush the year before. This photo was taken in winter. The foam contracted more than the wood frame allowing the frame to show.
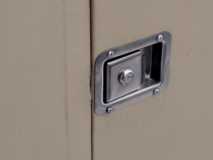
Re: XPS and Epoxy

Posted:
Thu Jan 05, 2023 10:51 am
by kstills
Pmullen503 wrote:See how the door frame shows? It was flush the year before. This photo was taken in winter. The foam contracted more than the wood frame allowing the frame to show.
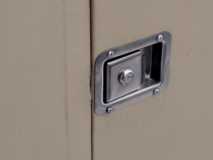
Explains it all.
I assume that was wrapped?
Re: XPS and Epoxy

Posted:
Thu Jan 05, 2023 11:00 am
by Squigie
Aircraft and hobby aircraft (RC) builders have been doing this for years. More recently, it has become a more popular forming method for custom auto body panels, as well (but usually with an acetone rinse afterward, to remove the foam and leave just the shell if it is the final panel).
I have never understood why PMF gets so much traction, other than (perceived) lower price point and fear of epoxy.
PMF'd foamies, to me, are like the modern homes in areas with no building code, or limited building code, where all of the anti-racking comes from an off-brand Tyvek wrap and siding installed directly onto the exterior wall studs. Sure, it saved a little money. But at what cost in lifespan and future maintenance?