I tried using my new hot wire cutter to cut some foam and was disappointed. It moved pretty slow (at least in my mind), threw smoke and fumes (I reduced most fumes with a vapor filter on my respirator), but the cut quality was low. Not like when I ran a small test piece over a single wire. To cut 2" thick foam, you need a 2"+ V-shaped piece of wire, which try as I might, was not perfectly in line and caused a cut line with two somewhat offset lines. I said screw it and set my circular saw to cut 2" and went to town.
The edge of my garage worked well for this, as the concrete in my garage is fairly flat, and there is a small drop-off where the concrete ends to give the blade space to stick through.
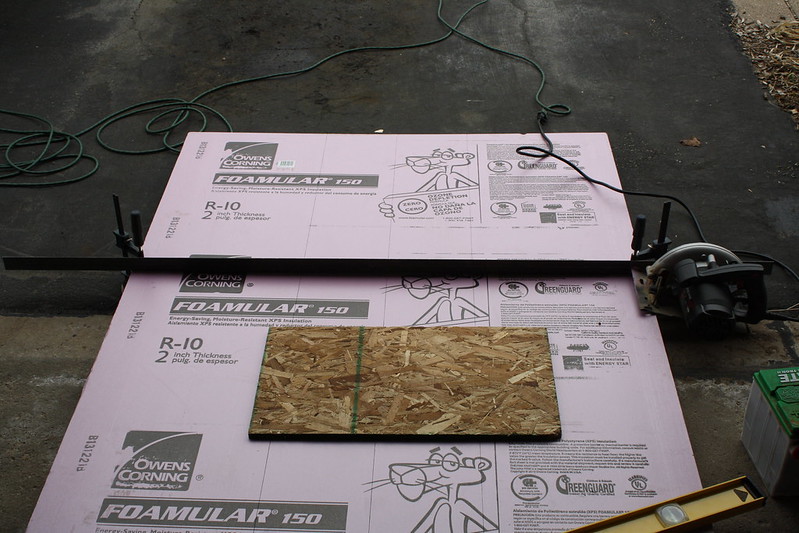
This method cuts a very smooth line very fast, it's like you're not even cutting anything. Lots of clingy foam dust! I cut two of the foam sheets to 5'6" long, to be used for the roof.
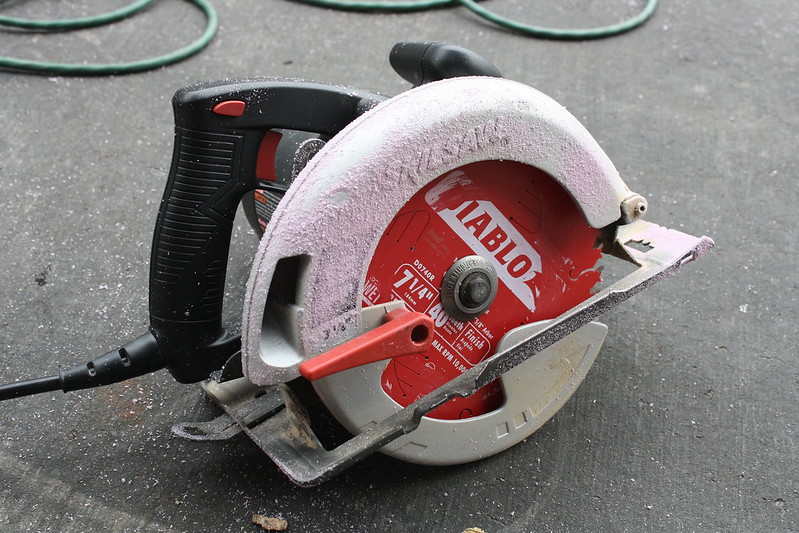
Since I "gave up" on the hot wire cutter, I kerfed with the circular saw. I set the depth to leave about a quarter inch or so, about what I had seen looking around on the forum and tried a test piece. I first cut a kerf every 4", bent it over my wall to see where that was good enough, marked the location, then cut middle lines to end up with 2" kerf spacing. I tried bending the piece on the wall again, noting where the 2" kerfs worked and where they did not, where I would need closer spacing.
My dad then arrived to help me, and with his help we kerfed two roof pieces. Using the marks I had, we kerfed one piece with 1" and 2" kerf lines, tested it, and changed a few more 2" lines to 1" lines as they weren't close enough. LOTS of dust! Especially on my dad, since as I made the cut it was throwing dust onto him. The two boards closest to the camera where for me to kneel on while cutting, the piece furthest away was the guide piece for the saw my dad would hold and then position again after each cut. It went fairly quick, you can run the saw as fast as you'd like, and he'd have the guide about positioned again by the time I had brought the saw back and lined it back up.
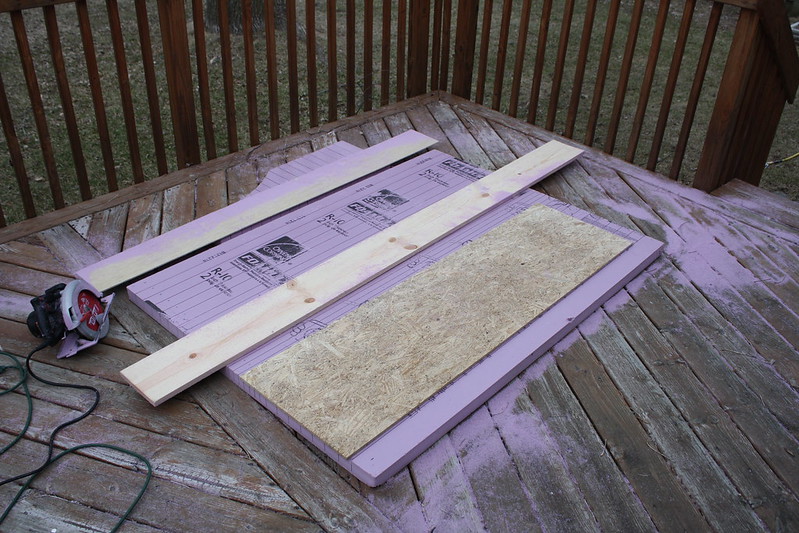
By the time we ate, kerfed both pieces, tested, and cleaned up, it was about time for him to go. I kept messing with the pieces after he left to get them ready to glue up. I still had to cut the beveled cut where the foam meets up at an angle with the straight front of the trailer. However, my circular saw could not cut the required ~33° angled cut and still get through the foam, it would leave about a half inch uncut. I tested cutting a piece on my tiny table saw, and it could cut all the way through the foam on my test pieces. However, after I tried holding up my roof piece, I realized there was no way I could guide this now floppy piece of foam through the table saw. So I cut it with my circular saw, then after some experimentation and thinking, I grabbed a handsaw and cut the rest of the cut with that. Worked out good, the circular saw cut acted as a guide.
Doing a test bend, I snapped the outside of the foam at one of the kerf lines about 2/3 down the width. Realizing I needed more strength, I thought back to building my RC airplane out of foam, and using packing tape to reinforce the foam skin to keep it from breaking. So I ran four strips of tape down the outside surface of the foam, opposite and perpendicular to the kerfs. Then, with my roommates help, we glued it up.
He held the foam, while I applied glue and water. After I had applied it, he started bending the foam near the bottom, and I ran strips of packing tape from the front of the TD to the walls, pulling as I attached them to the walls, which pulled the foam in and held it snug against the curve. I ran a strip of tape, a gap about as wide as a strip of tape, and so on. I taped up about half of one side, then the other side, and finished with the top half of the first side. I ran the glue in two sections as well, bottom and top halves.
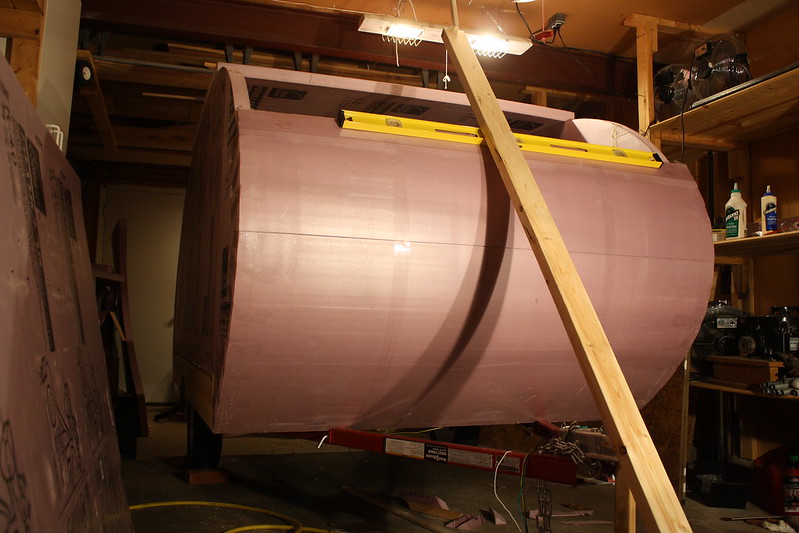
The 2x4, straightedge, and 1x2 (above the 2x4) are holding the top of the curve in a little bit. I noticed after we were done it was bowing out a little at the top, so I wanted to push it in, at least while the glue dried. This was actually my roommates suggestion, he said lean a 2x4 against it, but it didn't do much, so he said put a stick between the top of it and the ceiling, which pressed it down and worked quite well.
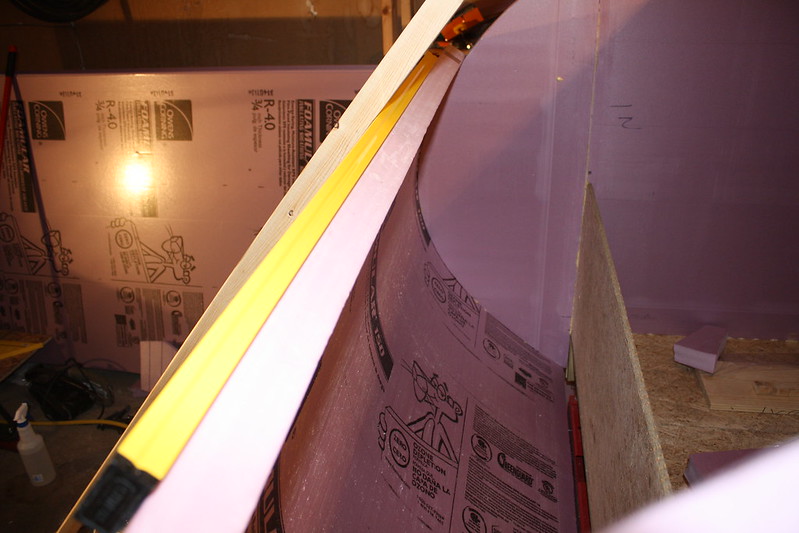
Using my dad's suggestion, I taped the second cut piece on top of the TD before I started gluing the front piece in. This positioned and spaced the walls at the top, to make sure they would end up at the proper spacing and helped align the front walls.
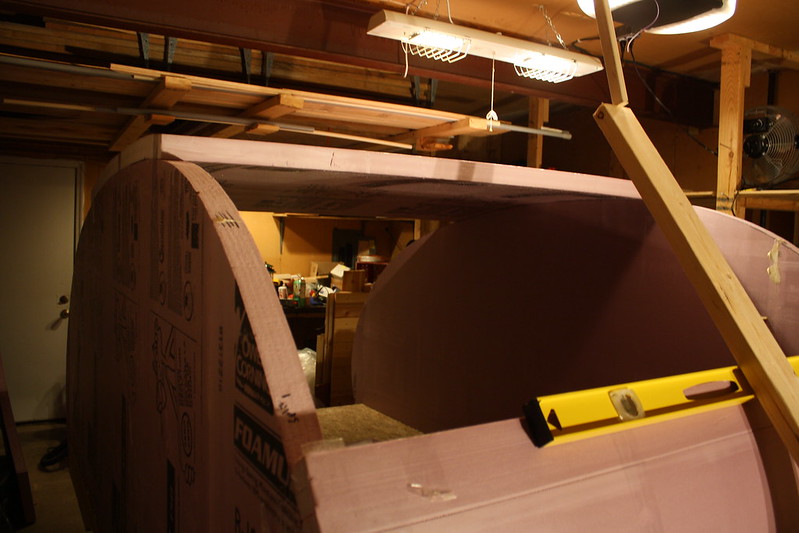
Here's another view of the inside of the curve. I did not apply any glue inside the kerf lines, I figured that the canvas I will apply inside and out will hold everything together fine.
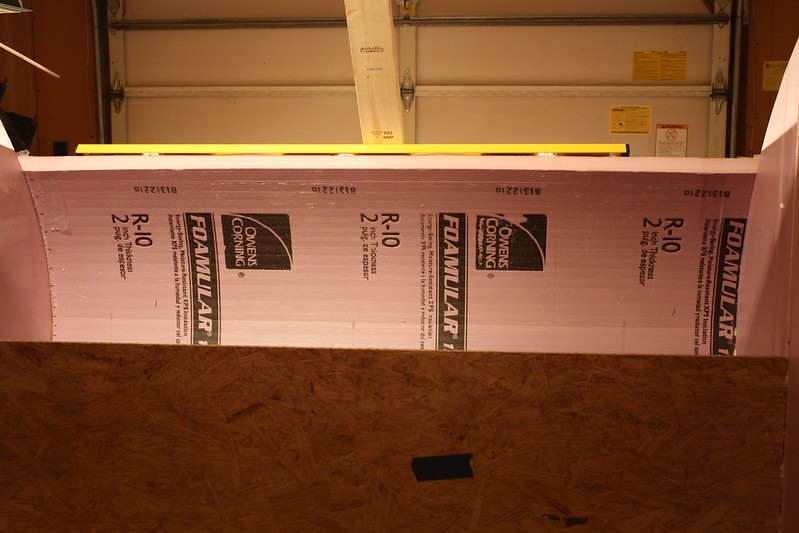
I will apply the next roof piece tomorrow. Good progress today.