I would suggest scarfing your panels together to make a sheet the size you need. The process is simple. Put an 8:1 (at a minimum - 12:1 is better) bevel on each sheet to be joined, and glue it together with thickened marine epoxy.
The advantage of a proper scarf joint is that it largely eliminates any stress riser or hard spots. The ply will curve and behave as if it we're a single piece.
There's multiple ways to do this. You can use a router with a fixture to guide it. You can use a plane (hand or power), a belt sander. A hand plane is simplest: stack the 2 workpieces to be scarfed face to face. Slide the top sheet back be 8, 10, or 12 times the thickness of the plywood. Start planing across the edge, taking a fine cut. The plus will guide you: if you're cutting a flat bevel, the plus will be of uniform thickness.
Put a piece of plastic on the assembly table. It doesn't have to cover the entire table, just a strip wide enough to protect against squeeze-out. Place one piece on the table with the bevel over the plastic.
Apply a coat of unthickened marine epoxy to each faying surface. Then mix another batch of marine epoxy, thickened with wood flour or fumed silica (structural thickeners, do not used microballoons). Apply a coat to the bottom piece. Address the top piece to the bottom piece. Put another bit of plastic over the top and clamp. You can use weights, but the easiest way might be to use a piece of scrap plywood or 1x stock large enough to more than span the entire joint on all sides. Drive some drywall screws through both pieces of ply outside of the joint and drive them home to draw the joint tight. Walk away until it cures. Remove the screws and clean up the joint. The screw holes can be plugged with more thickened epoxy. Use wood flour, as that will give you a wood colored plug.
https://boatbuildproject.com/scarfing-p ... and-plane/https://sandypointboatworks.com/boat-bu ... ng-joinery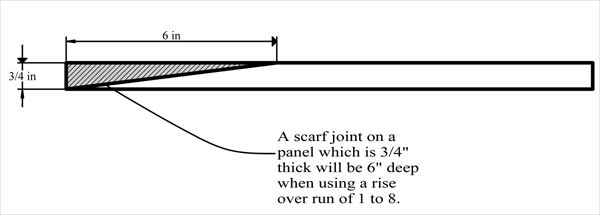
[youtube]https://youtu.be/P4cSEqyk_7A[/youtube]